Genuine Horween Shell Cordovan Leather
An American Tradition Since 1905
A century ago, Chicago was home to scores of famous tanneries. Today there’s only one: Horween Leather Company. For more than 100 years, this family-owned business has built a reputation for making truly exceptional leathers—in particular, their shell cordovan.
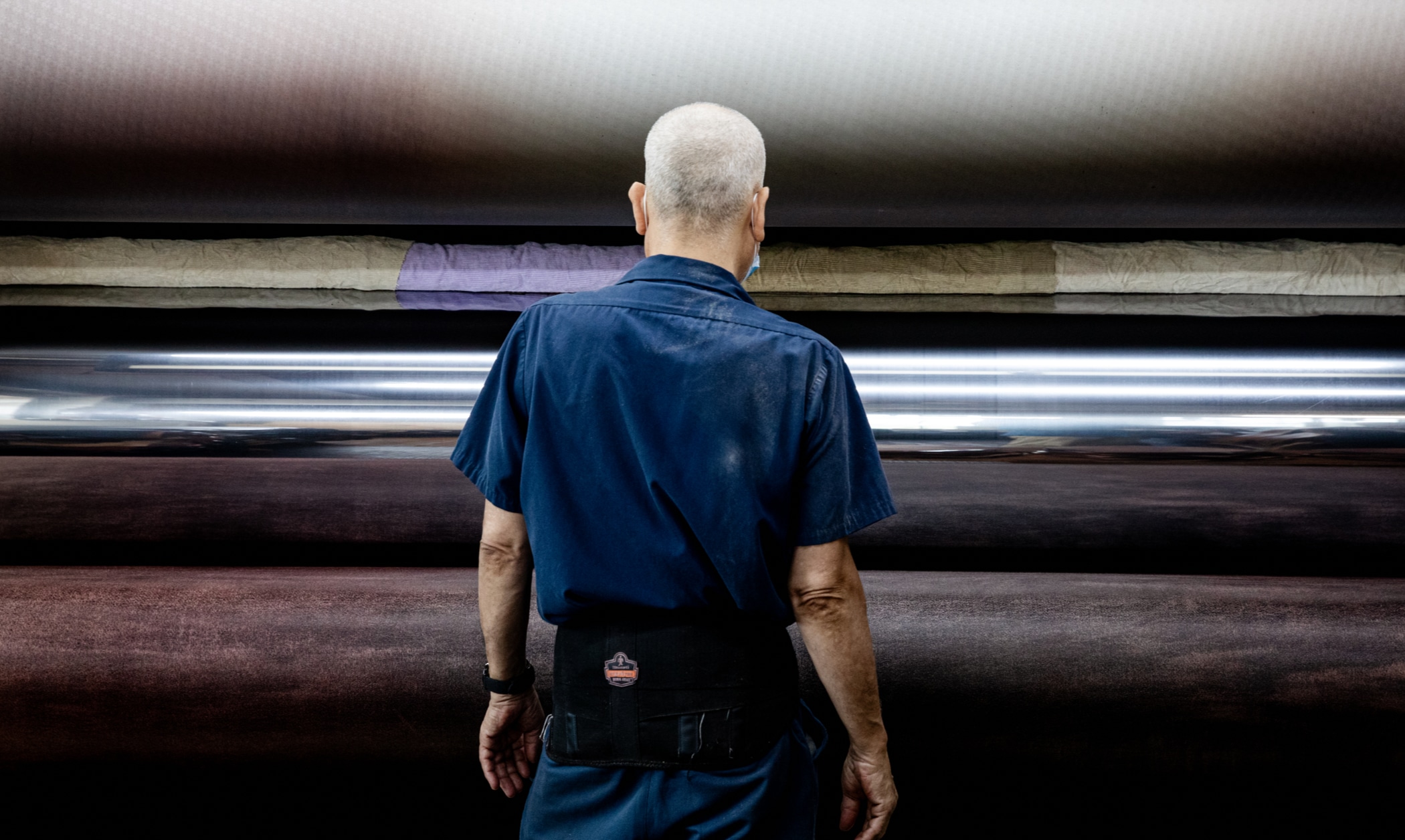
The Finest Shoemaking Material Passed Down Through Five Generations
Throughout history shell cordovan has earned a reputation as one of rarest, most sought-after leathers. Dense and strong so that it won’t develop creases like standard hides. Incredibly smooth with a tight surface structure and rich polish. Durable enough to last for decades, molding to the individual shape of your feet and developing a patina that’s unique to you over time. Those same qualities also make it one of the toughest materials to produce. Only the very thickest, rear sections of the hide can be used and tanning is a multi-month commitment where an error at any stage can ruin the final product. That’s where Horween’s singular expertise comes in. They use a signature, six-month process to create truly exceptional leather in a rich range of distinctive colors. Their lighter shades of cordovan—including natural and chili—are especially prized because they both showcase the natural beauty of the material and don’t allow for any imperfections./p>
Our Classic Styles Handcrafted in Horween Shell Cordovan Leather
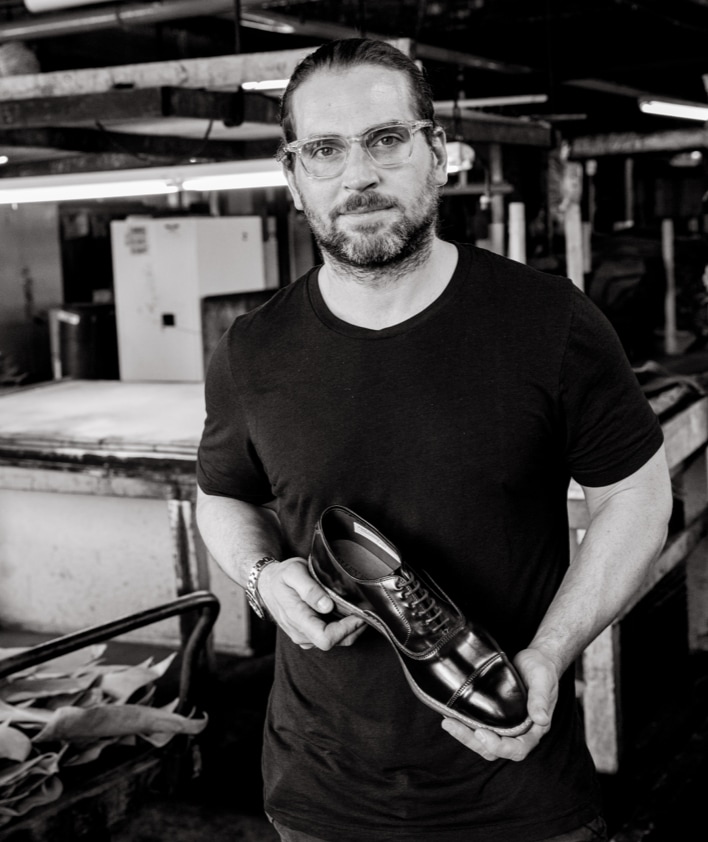
“When we first opened in 1905 all we made was cordovan, so my great-great grandfather came up with the processes and formulation and that’s basically been unchanged ever since.”
—Nick Horween, Vice President, Horween Leather Company
Before it became one of the most sought-after suppliers to shoemakers, Horween got its start producing shell cordovan for razor strops. These sturdy bands of leather were used to sharpen the blade of traditional straight razors prior to the invention of the safety razor. Shell cordovan was the perfect material because it was both abrasion-resistant and more dense than ordinary leathers.
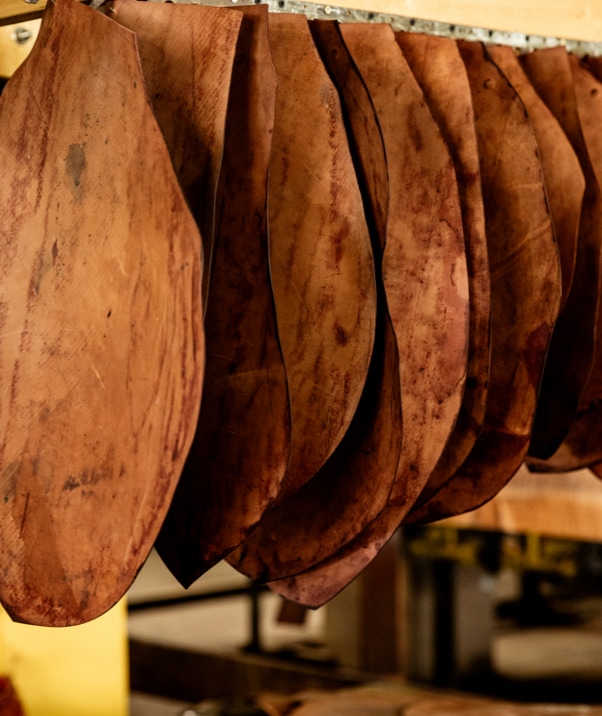
“The steeping process, that’s two months. Then we hand oil it and it needs to sit and cure for three months. Then the last month is a more active process where we’re dying and shaving and trimming. It just needs that much time. The shell is super dense which is why it’s a great leather.”
—Nick Horween
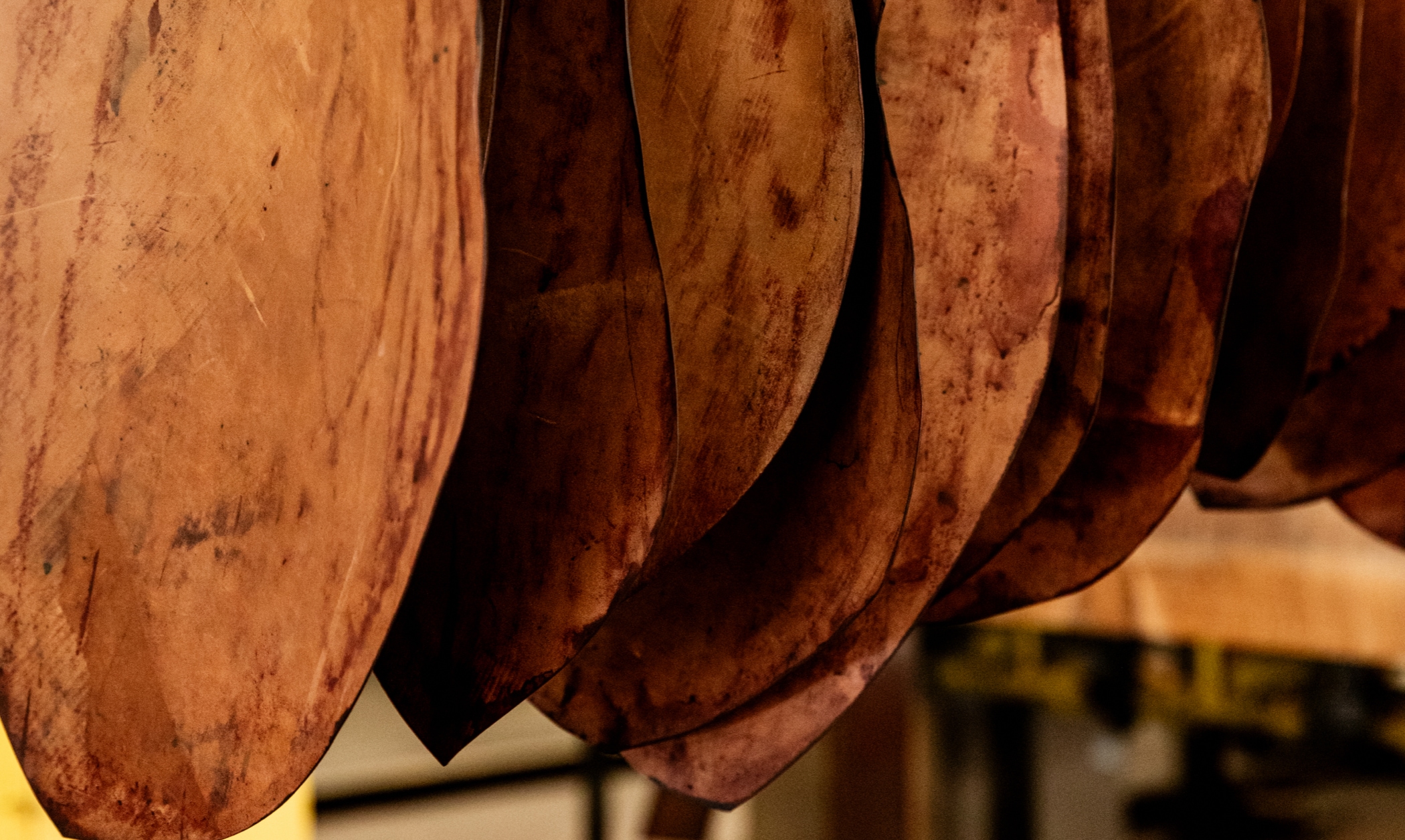
At Horween the commitment to tradition is built into the very foundation of the building. Many of the original tools and machines that produced shell cordovan over 100 years ago are still in use today. Some of the processes that demand particular precision, like the shaving of the hides, can only be completed by two highly skilled team members, each with decades of experience.
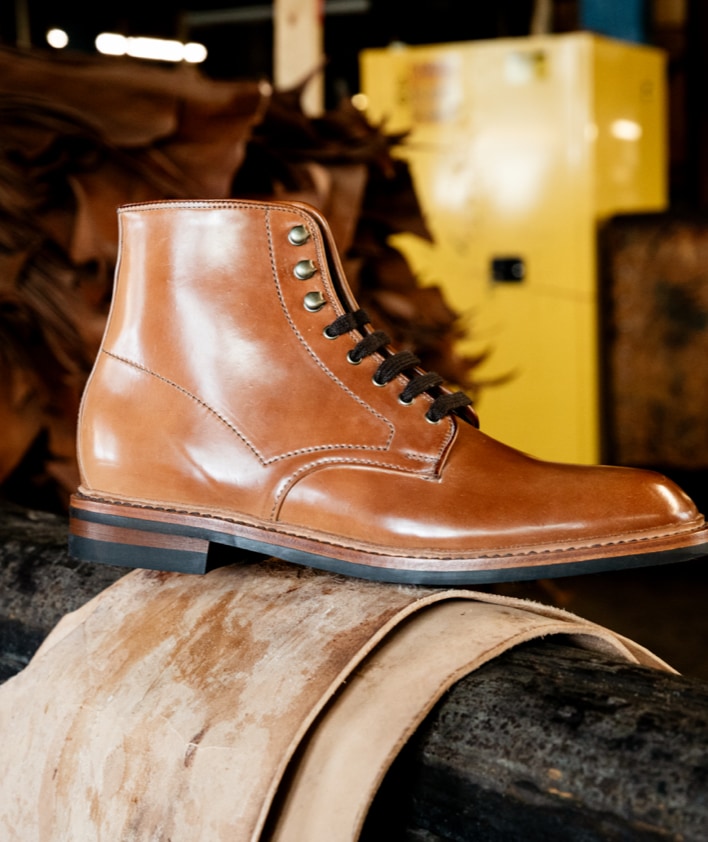
“You have to have a lot of experience to work with cordovan which is why you see the traditional shoemakers use it and none of the more modern companies. It doesn’t lend itself well to modern manufacturing. Once you’ve coaxed it into a final product, it will basically last forever.”
—Nick Horween
Every step of the process for making Horween shell cordovan is built around longevity. The tree barks and other natural materials used for tanning gradually strip all the perishable elements out of the hides, making it extra durable. Fats and oil are infused into the surface to give it a long-lasting suppleness, pliancy and glossy finish. Careful cutting and shaving ensure each piece has an even thickness that can stand up to years of wear.
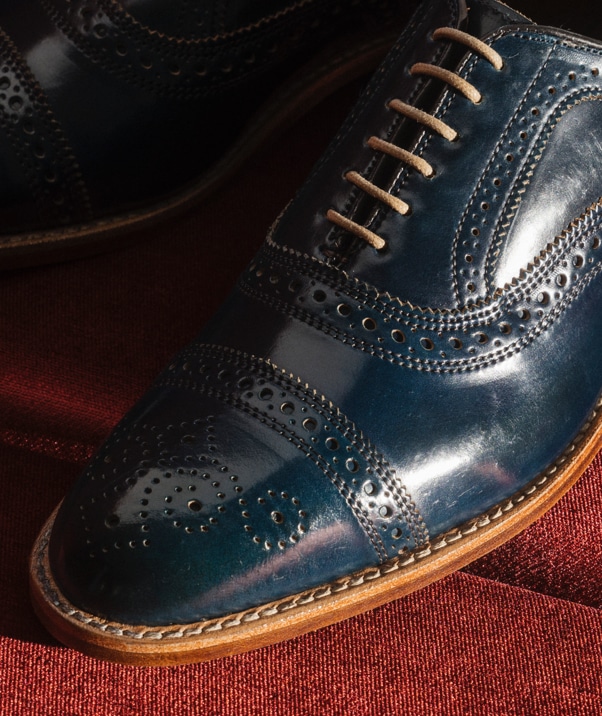
“It’s easy to make a usable product. It’s not hard to make something that’s mediocre. You can get 80% there but to get that last 20% is more work than the rest of the 80. We always aim for the 100% mark.”
—Nick Horween
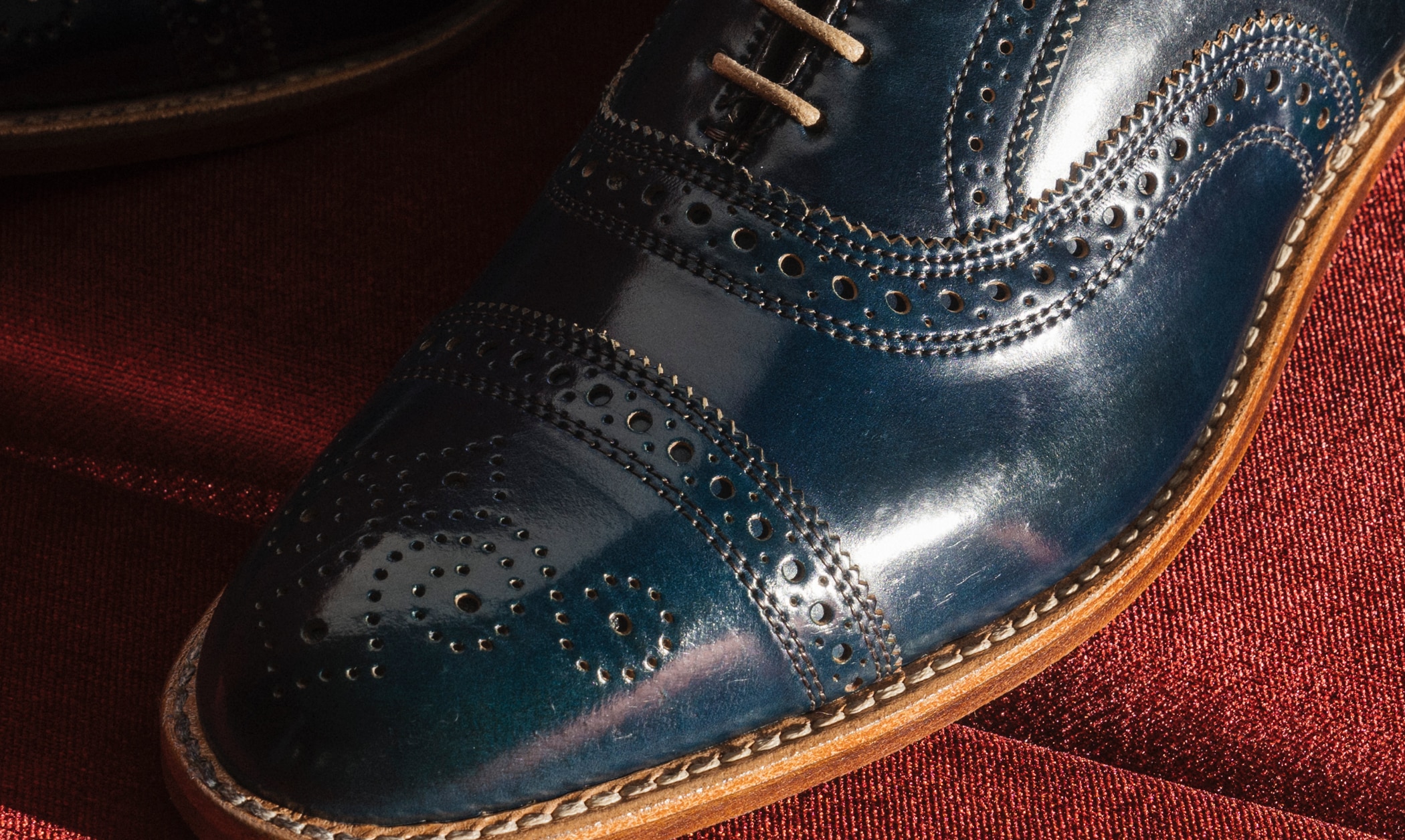